Company Visits
In the first and second week we will visit different leading companies in their business sectors in Munich and Southern Germany. During the company visits the participants will have the opportunity to see Operational Excellence at work, and will discuss company-specific topics with the managers in charge. The companies visited partly change very year, find a list of companies visited in previous years below.
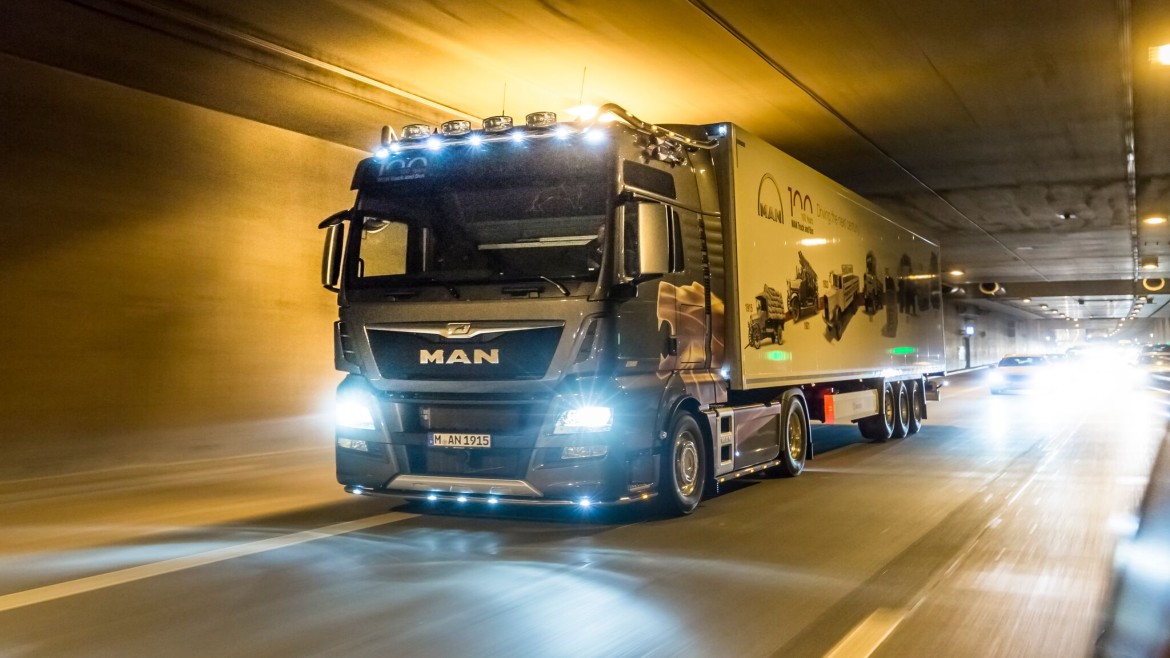
The MAN Group is one of Europe's leading commercial vehicle, engine and mechanical engineering companies, generating annual revenue of around 15.7 billion euros and employing a workforce of approx. 53,500 worldwide. MAN is a supplier of trucks, buses, diesel engines, turbomachinery and special gear units, with all corporate divisions holding leading market positions.
MAN Truck & Bus AG, which is based in Munich, Germany, is the largest company in the MAN Group and one of the leading international providers of commercial vehicles and transport solutions. The Revenue in 2013 was 9,05 billion euros, of which nearly 84 % are Trucks sales.
The company manufactures trucks with gross vehicle weights ranging from 7.5 to 44 tons, heavy-duty special-purpose vehicles with gross train weights of up to 250 tons, city and intercity buses and coaches, as well as diesel and natural gas engines. The Munich plant employed 8,600 workers in 2013.
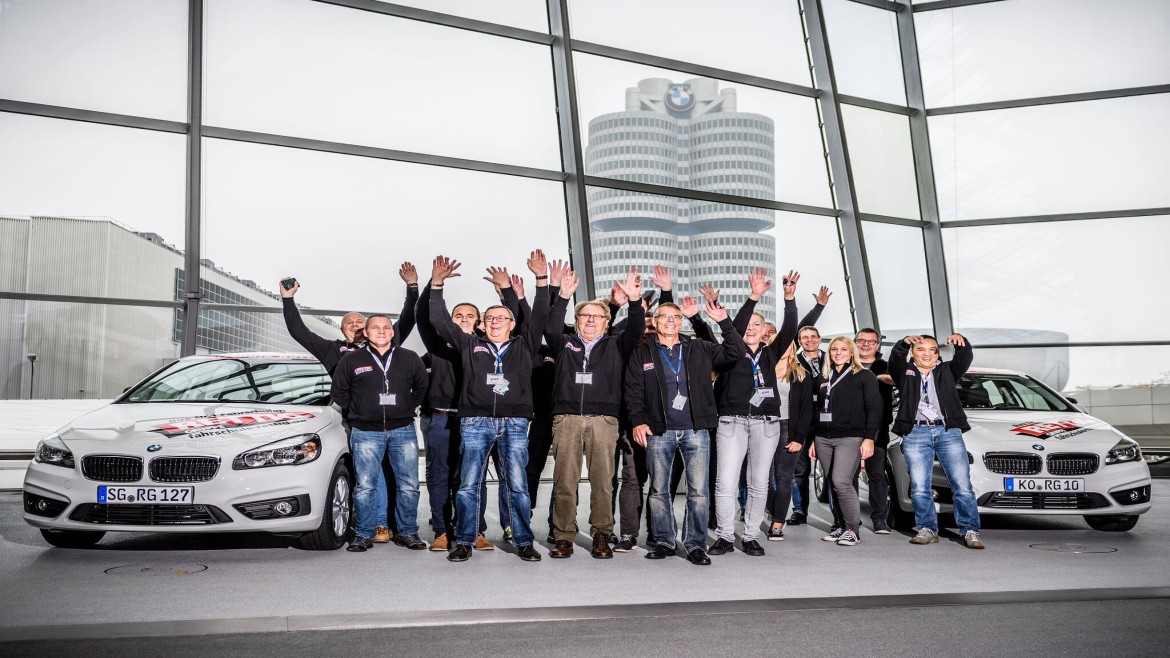
Founded in 1917, the BMW Group is now one of the ten largest car manufacturers in the world and, with its BMW, MINI and Rolls-Royce brands, possesses three of the strongest premium brands in the car industry. The company’s brand is extremely strong and is associated with high performance, engineering excellence and innovation. Indeed, the BMW brand is often cited as one of the ‘best’ in the world, and the company continues to launch a stream of innovative products as part of its battle with German peer Mercedes to be the world’s largest luxury car maker.
Plant Munich is the BMW Group’s parent plant. It combines supreme engineering and innovative strength with our people’s passion for the brand and the company. The plant is situated in the north of Munich, directly next to the Group’s Headquarters, the BMW Museum and the BMW Welt.
The workforce premises on the plant in Munich features 7.250 jobs. The BMW product range produced at the plant Munich spans from the BMW 3 Series to the BMW 4 Series and the BMW M4 Series. More than 950 vehicles are produced per workday.
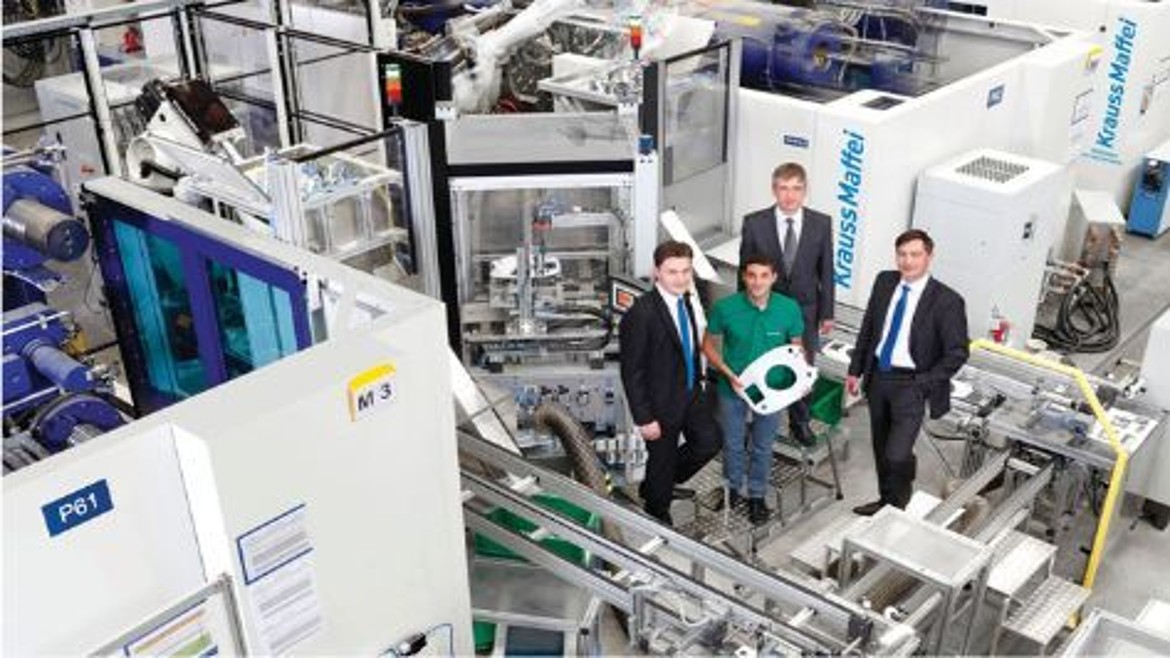
The KraussMaffei product brand is internationally synonymous with future-oriented and cross-technology system and process solutions in injection molding machinery, reaction process machinery and automation. As a complete supplier for all industries, KraussMaffei is characterized by its individual, modular or standardized products and a wide range of customized services.
As a system partner, KrausMaffei works together with customers to find the optimum system solution for them across all technology types - from the machine through process engineering to automation. The KraussMaffei Group, with its three product brands KraussMaffei, KraussMaffei Berstorff and Netstal, can thus cover the complete range in machine construction for the plastics and rubber processing industry and serve customers on an individual basis.
The KraussMaffei Group has ten production facilities throughout the world. The most modern methods and principles of lean production are used to build and assemble machines and systems. Injection molding machine production, for example, takes place in a synchronized assembly line. Evidence of production organized according to the pull principle can be seen through the entire value-adding chain up to the stringent control of the material flow of our suppliers.
In addition, the entire production process of the KraussMaffei Group is monitored by in-house Quality Management. The production philosophy is characterized by the continuous pursuit of improvements.
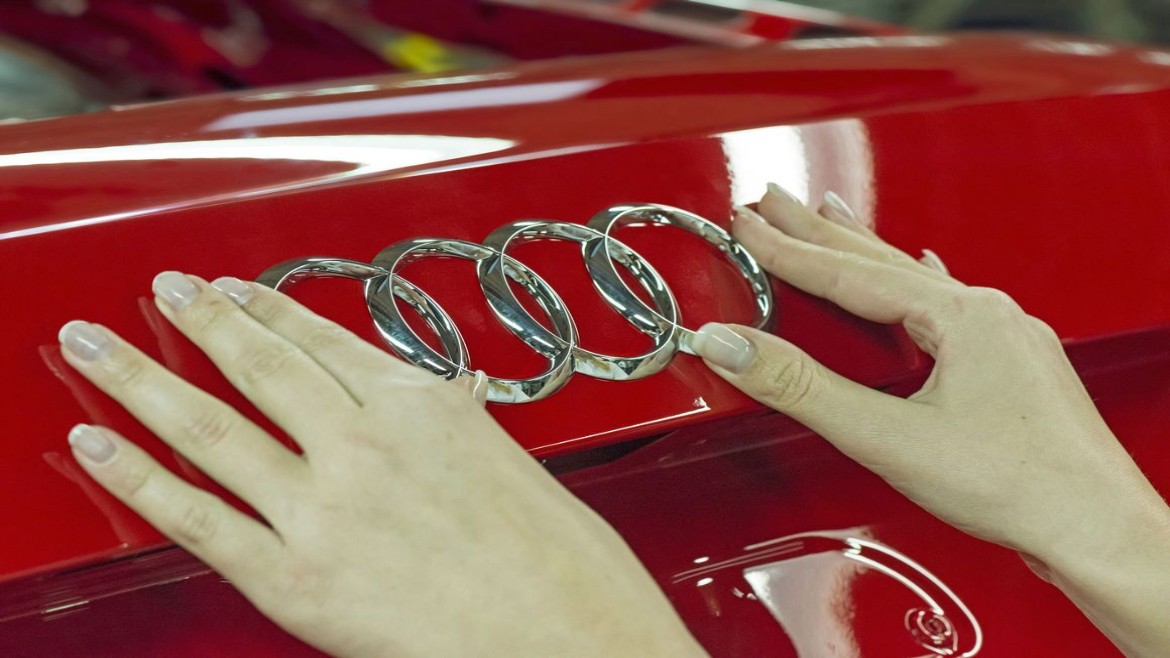
Audi AG is a German automobile manufacturer that designs, engineers, produces, markets and distributes luxury vehicles. Audi oversees worldwide operations from its headquarters in Ingolstadt, Bavaria, Germany. Audi-branded vehicles are produced in nine production facilities worldwide. The origins of the company are complex, going back to the early 20th century and the initial enterprises (Horch and the Audiwerke) founded by engineer August Horch; and two other manufacturers (DKW and Wanderer), leading to the foundation of Auto Union in 1932. The modern era of Audi essentially began in the 1960s when Auto Union was acquired by Volkswagen from Daimler-Benz. After relaunching the Audi brand with the 1965 introduction of the Audi F103 series, Volkswagen merged Auto Union with NSU Motorenwerke in 1969, thus creating the present day form of the company.
The company name is based on the Latin translation of the surname of the founder, August Horch. "Horch", meaning "listen" in German, becomes "audi" in Latin. The four rings of the Audi logo each represent one of four car companies that banded together to create Audi's predecessor company, Auto Union. Audi's slogan is Vorsprung durch Technik, meaning "Advancement through Technology". However, since 2007 Audi USA has used the slogan "Truth in Engineering".
Audi is among the best-selling luxury automobiles in the world. With 566,646 cars built in 2015, the Ingolstadt parent plant is the Audi Group’s largest production facility and Europe’s second-largest car factory. Globally networked, Audi Ingolstadt is the company’s flagship plant in terms of its technological prowess. This is where the Audi A3, Audi A4, Audi A5 and Audi Q5 car lines are built. In 2016, the production of the new Audi Q2 will also start here.
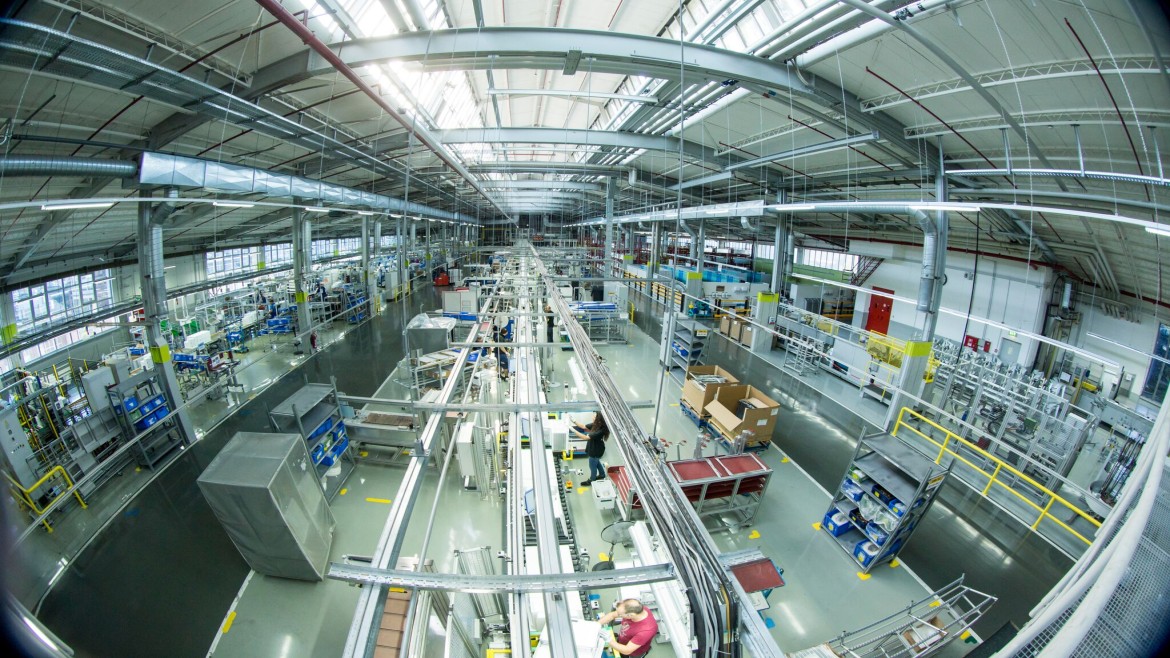
BSH Hausgeräte GmbH is the largest manufacturer of home appliances in Europe and one of the leading companies in the sector worldwide. With a portfolio of 14 brands, BSH covers a wide range of consumer needs. Alongside the Global Brands Bosch and Siemens as well as Gaggenau and Neff, the portfolio comprises the Local Heroes Thermador, Balay, Coldex, Constructa, Pitsos, Profilo, Ufesa and Zelmer, as well as the Label Brands Junker and Viva. Founded in 1967 as a joint venture of Robert Bosch GmbH (Stuttgart) and Siemens AG (Munich), BSH has belonged exclusively to the Bosch Group since January 2015.
With more than 56,000 employees, BSH increased its revenue in 2015 to around 12.6 billion euros. BSH has some 40 factories worldwide and produces the entire range of modern home appliances. This ranges from cookers, ovens and extractor hoods, dishwashers, washing machines, dryers, fridges and freezers to small appliances (Consumer Products) such as vacuum cleaners, coffee machines, kettles, irons and hairdryers.
The factory in Giengen was opened in 1944. Production of refrigerators and freezers started in 1949, so the plant has a long tradition behind it and can look back on countless innovations. This production plant, together with its Logistics Division, is the largest local employer and an important factor in the economy of both the town and the region. All BSH’s research and development activities in connection with refrigeration appliances are globally coordinated and managed from here.
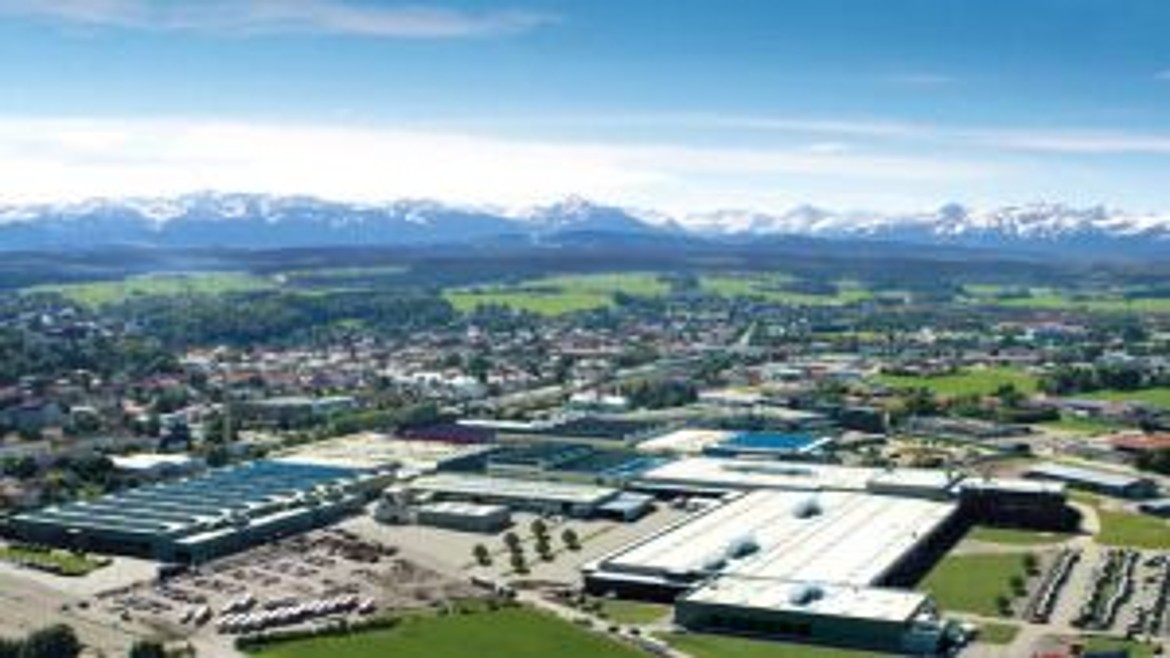
The AGCO Corporation is a major worldwide manufacturer and distributor of agricultural equipment. AGCO offers a full product line including tractors, combines, hay tools, sprayers, forage equipment and implements through more than 3,000 independent dealers and distributors in over 140 countries. Fendt is the corporation's new high-tech brand for highest demands. To keep the promise of high-quality to the customers every day, the production area works continuously on manufacturing perfect tractors. Quality control takes place daily, constantly and without interruption. Before a tractor leaves the factory, it is tested in various “Quality Gates” along the assembly line. In addition, the Management meets with the responsible supervisors three times a day, in the so-called Shop Floor Management Rounds, to compare the actual values with the target values - right in the middle of the production area, where everything takes place. This enables very short decision-making paths and an extremely fast reaction capacity.
With 30,200 employees worldwide ACGO achieved total sales of €8.5 billion in 2014. The Fendt cabs are assembled just-in-sequence in the new assembly hall at the Bäumenheim site and are delivered directly into the assembly process in Marktoberdorf. After unloading the truck, the cabs are put on the materials handling equipment. The overhead conveyor automatically brings the cab into position over the appropriate tractor body and lowers it precisely into place.
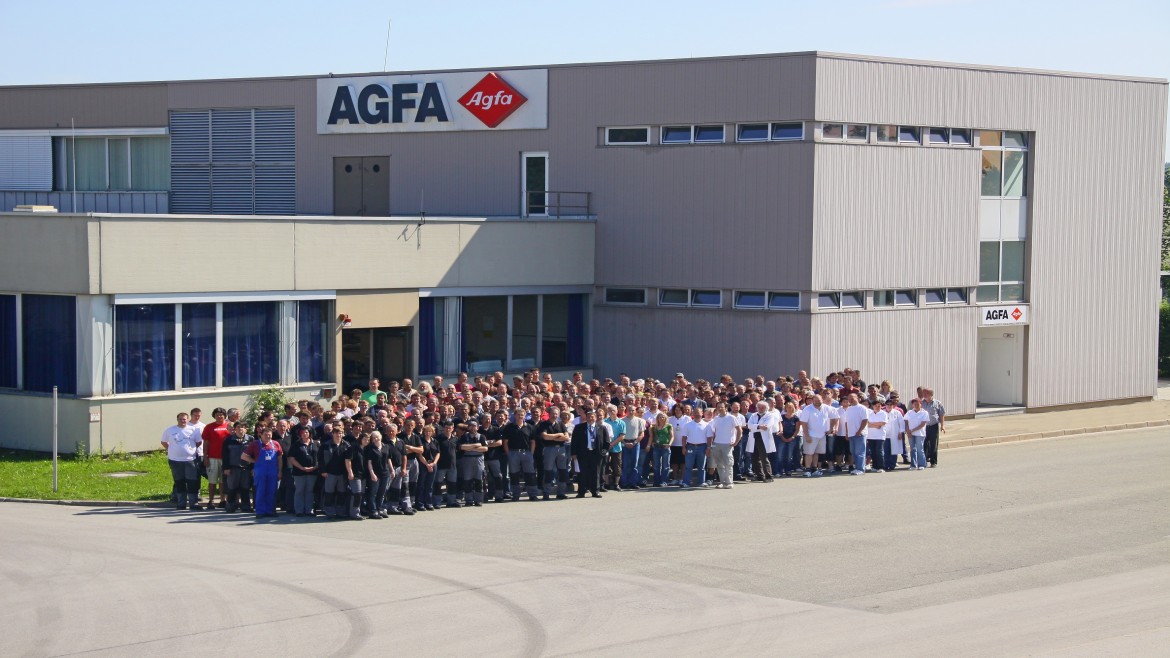
Agfa HealthCare is a leading provider of diagnostic imaging and healthcare IT solutions for hospitals and care centers around the world. The business group is a major player on the diagnostic imaging market, providing analog and digital technology, as well as IT solutions to meet the needs of specialized clinicians. The business group is also a key provider on the healthcare information solutions market, integrating the administrative, financial and clinical workflows of individual hospitals and hospital groups.
Today, care organizations in over 100 countries rely on Agfa HealthCare’s leading technologies, solutions and services to optimize their efficiency and improve delivery of patient care.
Peißenberg is the only production site of the Division Agfa HealthCare and has a workforce of about. 400 employees. It won the renowned competition of “Best factory of the year” several times.
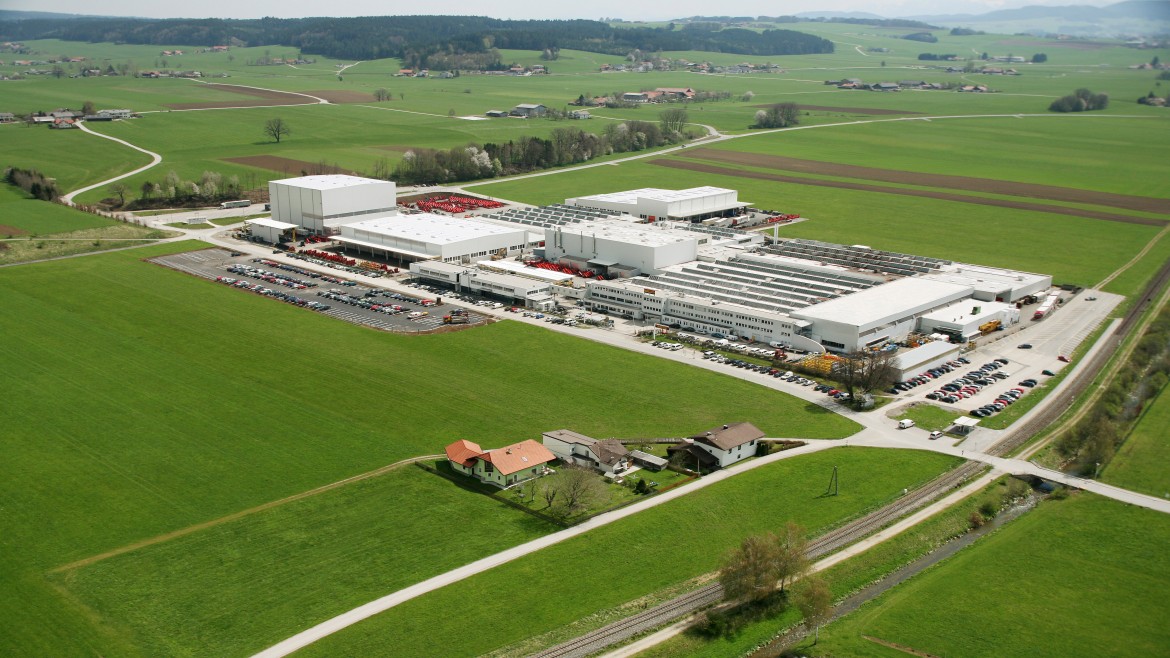
PALFINGER Europe GmbH in Lengau is the largest production location within PALFINGER AG and started operation in 1984. The main highlight is the production and assembly of cranes with a lifting capacity of 13mt to 78mt. As a mixed plant, which means a production and assembly plant, it represents the latest technology within the group.
The KTL plant has been in operation since 2002, for special surface treatment of the cranes. Since 2007 the hexagonal profile production facility has been in op-eration for production of jibs and extension profiles. The Lengau site is one of two spare parts centres for the processing of spare parts supplies.
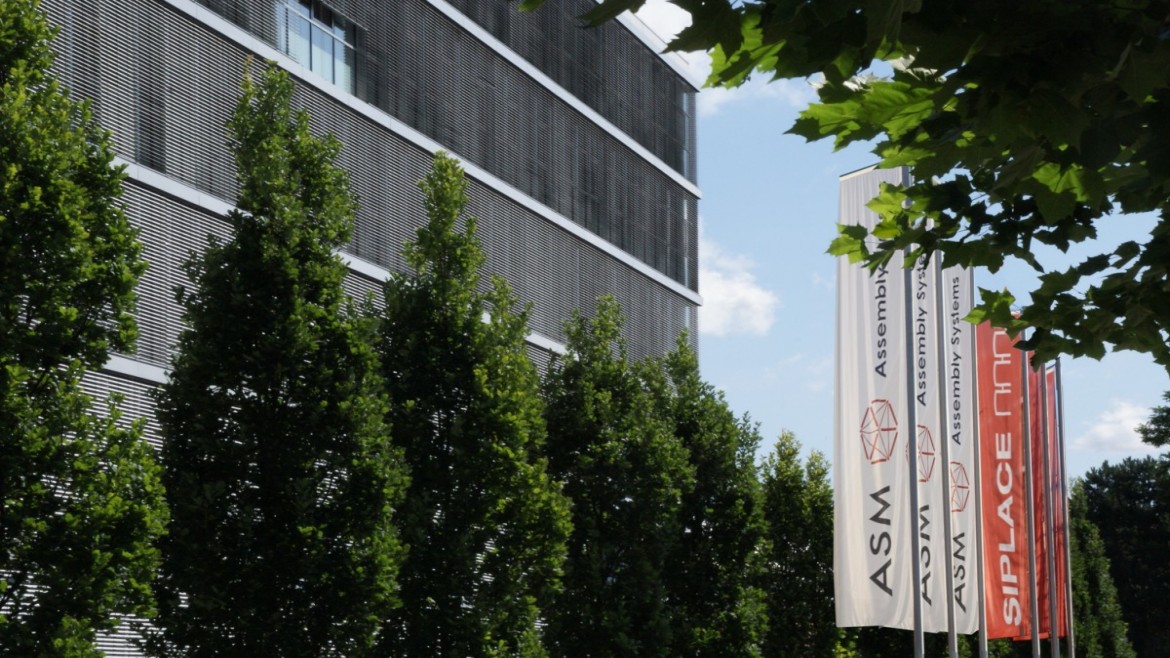
ASM Assembly Systems GmbH & Co. KG is a subsidiary of ASM Pacific Technology Ltd. Within the group, ASM Assembly Systems represents the SMT Solutions business segment with the business divisions SIPLACE Placement Solutions and DEK Printing Solutions.
Think globally, act locally – with its global cluster organization, ASM Assembly Systems provides its customers all over the world with quick and around-the-clock access to development, sales, service and support resources in their respective regions. The organizational structures and procedures in the regional structure are based on global standards.
The history of the SIPLACE team goes back to 1948. With its innovative manufacturing solutions, the SIPLACE team played an important role in the rapid development of the electronics industry – first as part of Siemens, and since 2010 as the ASM Assembly Systems business unit within the ASM Group.
The company introduced the first placement machines carrying the SIPLACE name in 1993. Since then, innovations have steadily pushed the limits of what's possible in order to squeeze ever more powerful electronics into increasingly smaller components. Today, electronics are produced on tens of thousands of SIPLACE placement machines all over the world.
The headquarters of ASM Assembly Systems is in Munich. This is also where the hardware and software for the state-of-the-art SIPLACE placement solutions are developed and tested before being custom-produced in the award-winning factory.
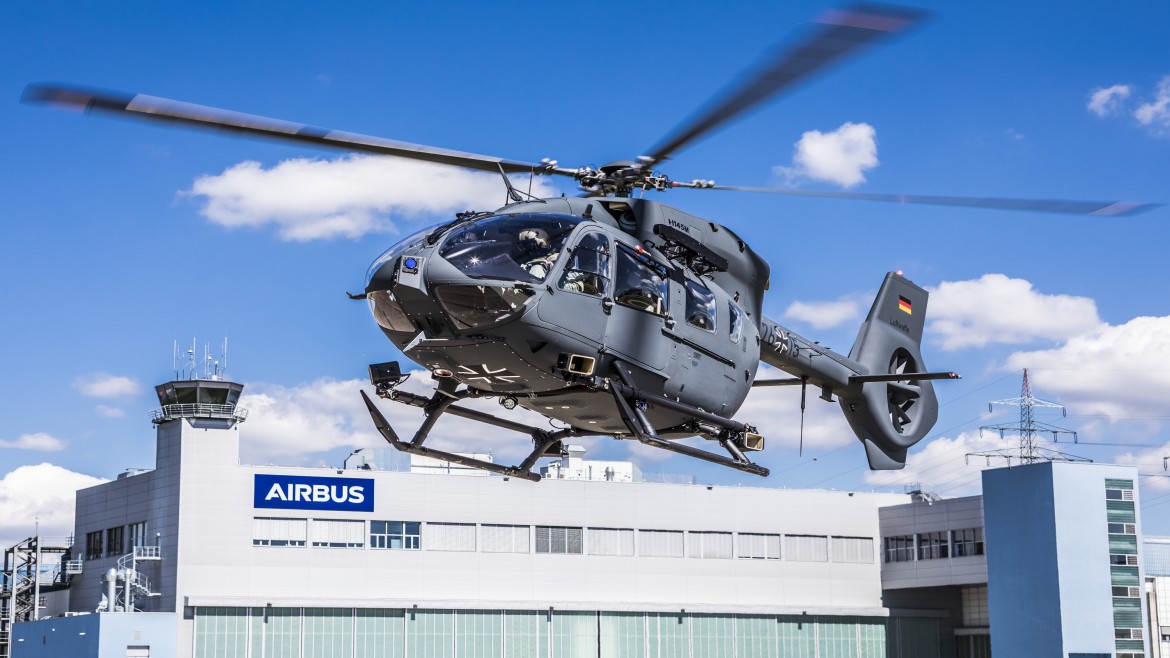
A commercial aircraft manufacturer with Space and Defence and Helicopters divisions, Airbus is the largest aeronautics and space company in Europe and a worldwide leader. As the world’s No.1 helicopter manufacturer, Airbus provides the most efficient civil and military helicopter solu-tions to our customers who serve, protect, save lives and safely carry passengers in highly demanding environments.
Airbus’ helicopter fleet in service includes some 12,000 helicopters operated by 3,000 plus customers in 154 countries. The helicopter division’s international presence is marked by its 29 customer centres and participations and its worldwide network of service centres, training facilities, distributors and certified agents. More than 22,000 people worldwide are employed by Airbus Helicopters.
The factory in Donauwörth employs about 7000 workers and is one of the most important companies in the region Donau-Ries.
Activities in Donauwörth:
- Research & Development
- Test flight / prototype & serial
- German Head office
- Composite & Mechanical and Blades mechanical centre
- Delivery
- Assembly line
- Customer service
- Training centre
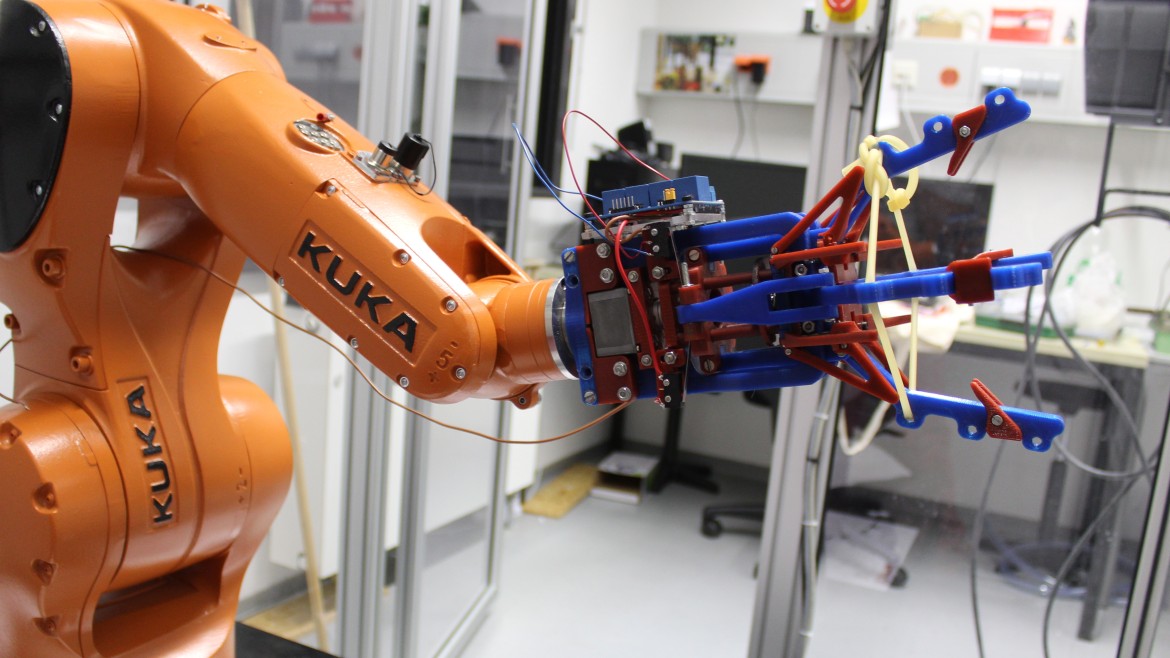
KUKA is one of the world’s leading suppliers of intelligent automation solutions. 13,200 employees at the headquarters in Augsburg and around the world produce sales of around 3 billion euro per year.
KUKA customers come essentially from the automotive industry and general industry. KUKA offers everything from a single source: from the individual components to fully automated systems. KUKA's portfolio offers matched automation solutions for more efficient manufacturing processes – from just a single robot to specialized cells through to complete system concepts.
For the automotive industry, KUKA is the world's leading provider of production systems in the automotive industry. In e-commerce and retail logistics, the KUKA Group offers flexible, robotic automation solutions characterized by utmost flexibility, speed and availability. For the electronics industry, KUKA offers preconfigured packages consisting of robots, innovative software and efficient control technology for a more flexible production.
The Krones Group, headquartered in Neutraubling, Germany, plans, develops and manufactures machines and complete lines for the fields of process, filling and packaging technology. Its product portfolio is rounded off by information technology, factory planning and products from Krones’ subsidiaries as intralogistics, valve production etc.
Since being founded in 1951, Krones has become far more than a traditional-style machinery and line manufacturer: it has evolved into an all-round vendor for its clients. Mechanical engineering, line expertise, process engineering, microbiology and information technology have here been harmoniously integrated for optimum synergies. Nowadays, Krones is synonymous with holistic systems engineering.
Krones’ success is based on some few but crucial strategies: specialised knowledge of mechanical engineering and the customer sectors involved, a technical lead over its competitors driven by continuingly high expenditure on research and development, production facilities featuring state-of-the-art equipment operating to the most strin-gent of quality standards, backed up by worldwide 24/7 service support, and most especially by the skills of its highly motivated staff. About 5,500 full and utility patents bear witness to the company’s innovative potential.