Research Project
Consideration of sequence effects in service life estimation of hollow section joints
Prof. Dr.-Ing. Andre Dürr
Department of Civil Engineering
Prof. Dr.-Ing. Klemens Rother
Department of Mechanical, Automotive and Aeronautical Engineering
Structures made of hollow sections together with high-strength steels have great economic potential due to their possible application as lightweight solutions. Joints of frames and trusses made of hollow tubular sections are preferably used in commercial vehicles, steel construction, cranes and agricultural machinery as well as in the energy sector like wind turbines.
Tubular structures are often subjected to fatigue stresses. Structural joints used in vehicles, cranes or bridges are subjected to cyclic loading which might cause fatigue failure. Fatigue of welded tubular structures therefore might be a fundamental cause for damage of these lightweight designs.
Fatigue strength and S-N-curves for tubular joints have so far been derived from constant amplitude testing mainly on low strength steels. The transfer to real variable amplitude loading from service conditions to proof structural integrity analytically usually is carried out using damage-equivalent constant amplitude load spectra based on the simple Palmgren-Miner rule with a generalized limit value of D=1.0 irrespective of material strength and load spectra shape.
However, this method does not take into account advantageous and disadvantageous load sequence effects from real operating load spectra. Various studies show that the linear damage accumulation rule according to Palmgren-Miner, which is very simple in its application, rule is often inaccurate in its original or slightly modified versions. The IIW-recommendations and FKM-guideline already recommend a conservative limit damage sum of D = 0.5 to compensate systematic errors in the quality of prognosis. This inevitably leads to significantly heavier or unsafe design solutions and thus contradicts the aim of a consistent lightweight design.
The object of this research project is to investigate the influence of realistic variable amplitude load spectra including sequence effects on lifetime estimation of welded tubular structural joints, dependant on manufacturing conditions for low- and high-strength steels. Using realistic applications from (thin walled) commercial vehicles as well as (thick walled) cranes the results of this research project will have impact on a wide range of industrial applications. Thus, knowledge on the influence of size effects is also obtained within the project. Experimental studies are carried out on typical details of welded tubular joints using various realistic operating load spectra and two-stage load spectra. These experiments will serve as a basis for improving the analytical assessment methods.
Aims of the research project:
- Experimental based investigation of the influence of realistic load and stress spectra including sequence effects on the lifetime estimation of welded tubular joints
- Investigations depending on production conditions, size influence and material to ensure transferability to larger structures.
- Derivation of correction factors from variable amplitude loading applied to known analysis methods to improve lifetime estimation.
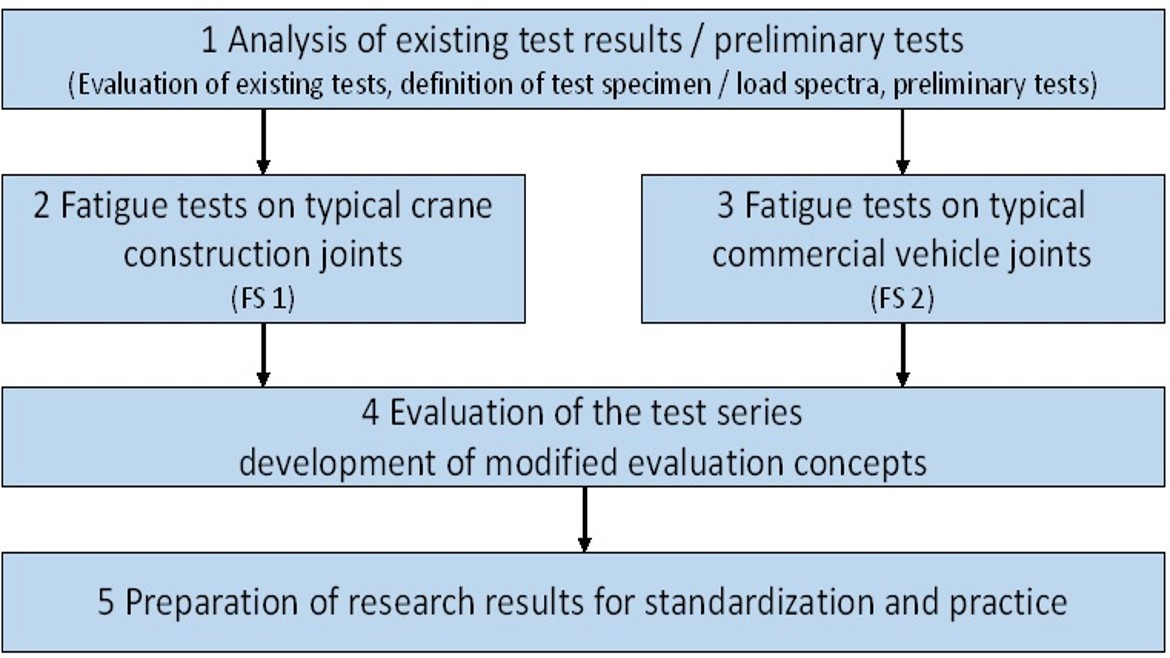
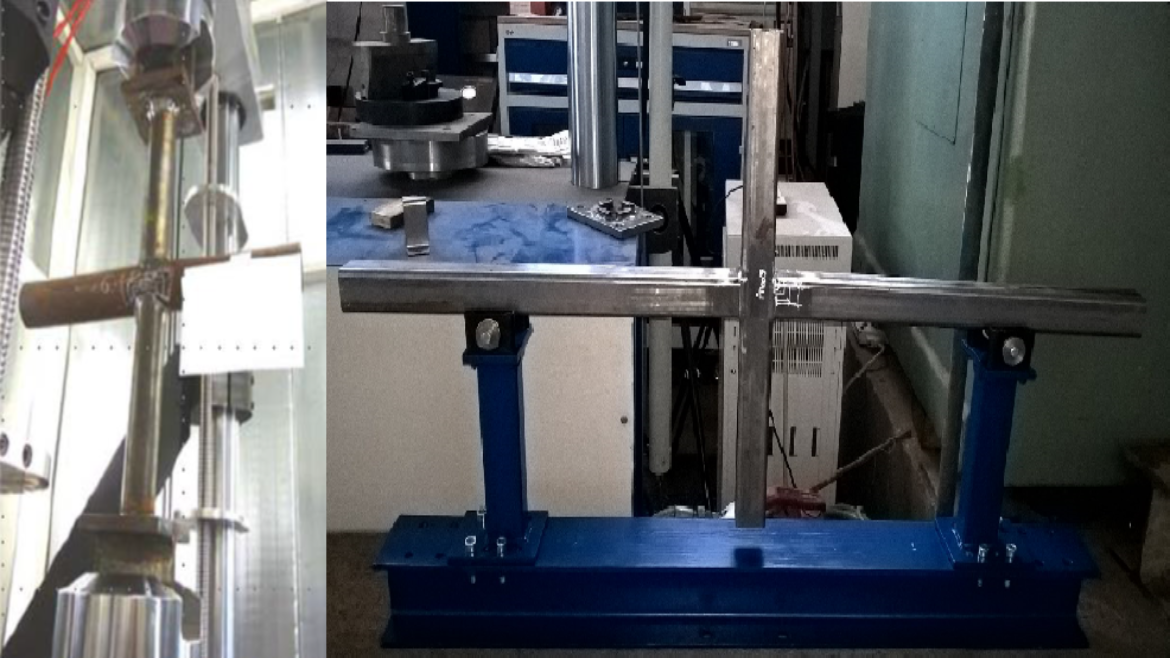
Running duration:
01.04.2017 - 31.03.2020, extended until 31.03.2021, extended until 30.09.2021
Funded by:
Federal Ministry for Economic Affairs and Energy
Project executing organisation:
Federation of Industrial Research Associations
Research Association Steel Application e.V.