Research Projekt
Modified fatigue strength verification of untreated and HFH post-treated welded constructions, taking collective form, stress ratio and notch details into account
Prof. Dr.-Ing. Imke Engelhardt
Department Civil Engineering
Initial Situation:
The extension of the service life of structures and the development of resource-saving constructions represent current challenges of civil and mechanical engineering. Many of these constructions are subject to variable loads, so that the fatigue strength of decisive, highly stressed components, the so-called notch details, is relevant for the design. It is therefore important to find approaches to determine the service life realistically and economically and, if necessary, to extend it.
For welded constructions subject to fatigue, the reliability of damage accumulation hypotheses and the applicable damage sums is called into question, so that a reduction of the permissible damage sum to values of D≤0.5 is recommended in regulations. Regardless of the influences of collective shape, medium stress, notch detail and notch sharpness as well as the influence of post-treatment methods on the permissible damage amount, this overall reduction of the damage amount leads to a significant increase of sheet thickness for constructions with a high number of load cycles and thus less economical constructions.
Variable load studies show that the collective shape, changes in mean stress and the notch severity influence the result of the damage sums or the failure loads of weld seams. Ongoing research also shows that residual compressive stresses and hardening effects introduced by weld seam treatment processes are influenced by operating loads.
Methodology:
At present, however, there are no engineering models for taking into account for the influences on service life mentioned above. For this reason, the aim of this research project is to empirically derive influencing factors on the tolerable variable loads and develop calculation approaches using a probabilistic model based on two-stage crack and crack propagation calculations that contribute to the design of safe, economical and resource-saving constructions. Fracture mechanical methods for the crack propagation calculation of weld seams taking into account the collective shape, mean stress changes, notch sharpness and the condition of the surface layer through mechanical post-treatment have to be verified.
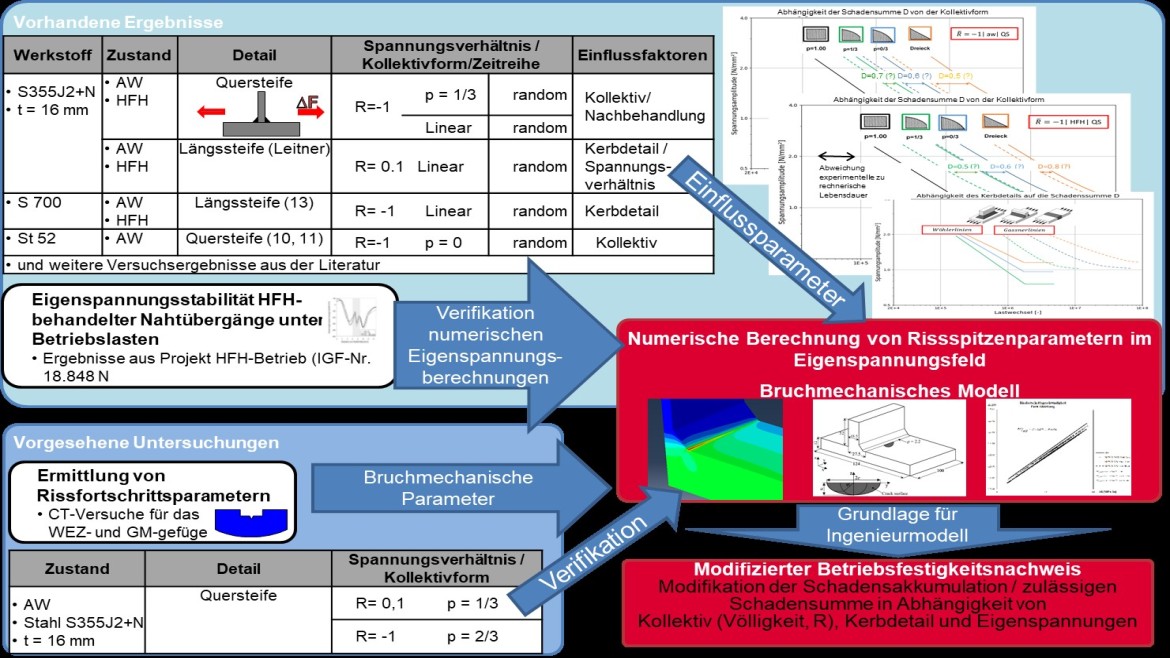
The aim is to develop an engineering model for the realistic estimation of the service life of welded and possibly post-treated constructions under variable loading, which takes into account the influences of collective shape, mean stress changes, notch sharpness and the condition of the surface layer influenced by mechanical post weld treatment.
Running duration:
01.04.2020 - 30.09.2022
Funded by:
Federal Ministry of Economics and Climate Action
Project executing organisation:
Arbeitsgemeinschaft industrieller Forschungsvereinigungen, AiF
Forschungsvereinigung Schweißen und verwandte Verfahren e. V. des DVS
Members of the Project Support Committee:
- Bundesanstalt für Wasserbau
- Bundesanstalt für Material und Bauforschung
- DNV GL –Maritime
- Framatome GmbH
- Franz Prebeck GmbH & Co KG
- HiFIT Vertriebs GmbH
- IBUKO Ingenieurgemeinschaft
- Jörss Blunck Ordemann GmbH, Beratende Ingenieure
- Krebs und Kiefer, Beratene Ingenieure für das Bauwesen GmbH
- Maurer SE
- Offshore Wind Technologie GmbH
- PITEC Deutschland GmbH
- Schachtbau Nordhausen GmbH
- Schuler Ingenieurbüro für Bautechnik
- Sennebogen Maschinenfabrik GmbH
- Siemens Gamesa Renewable Energy GmbH