Research project
InnoTurbinE
Joint project: Innovative turbomachinery for sustainable energy systems. Subproject: Fiber optic probes for high temperature measurements in gas duct
Prof. Dr. Johannes Roths
Department of Applied Sciences and Mechatronics
Innovative turbomachines are indispensable for the success of the targeted CO2 reduction in Germany's energy supply. Challenges for modern gas turbines are the increase in energy efficiency, the increased fuel flexibility (e.g. the increased use of hydrogen) and the improved load flexibility. The latter is necessary, for example, to compensate for the high variability of renewable energies in the power supply. Munich University of Applied Sciences is involved in the new developments of the turbomachines as part of the InnoTurbinE joint project, which is being carried out by AG Turbo, an association of world market leaders in the turbomachinery industry and German universities, and is funded as part of the German government's 7th Energy Research Programme.
In the sub-project "Fibre-optic probes for high-temperature measurements in the gas duct", which is being carried out in close cooperation between the HM Laboratory for Photonics and MTU Aero Engines AG, fibre-optic sensors are to be developed that will enable novel experimental investigations on gas turbines to increase their efficiency.
For measuring the total temperature in the gas channel, probes with stagnation tubes (Kiel heads) are installed. Using fiber optic sensors, total temperature profiles with 15 - 20 measuring points will be resolved with high precision for the first time. Compared to conventional single point temperature sensors, fiber optic sensors have a larger number of measuring points and a considerably lower cabling effort due to their multiplexing capability.
In particular, so-called fiber Bragg gratings (FBG) are used, which allow an application up to 700°C by a high temperature regeneration process. These sensors are developed with a laser-based process in the Laboratory for Photonics at the University of Applied Sciences Munich. The measuring point density shall be increased by reducing the RFBG length down to ≤1mm and the distance down to ≤2mm.
Assembly and mounting techniques are being developed to operate the optical fiber in the gas duct of the turbine. To estimate the influence of the assembly techniques on the measurement result e.g. through heat conduction, FEM simulations will be performed.
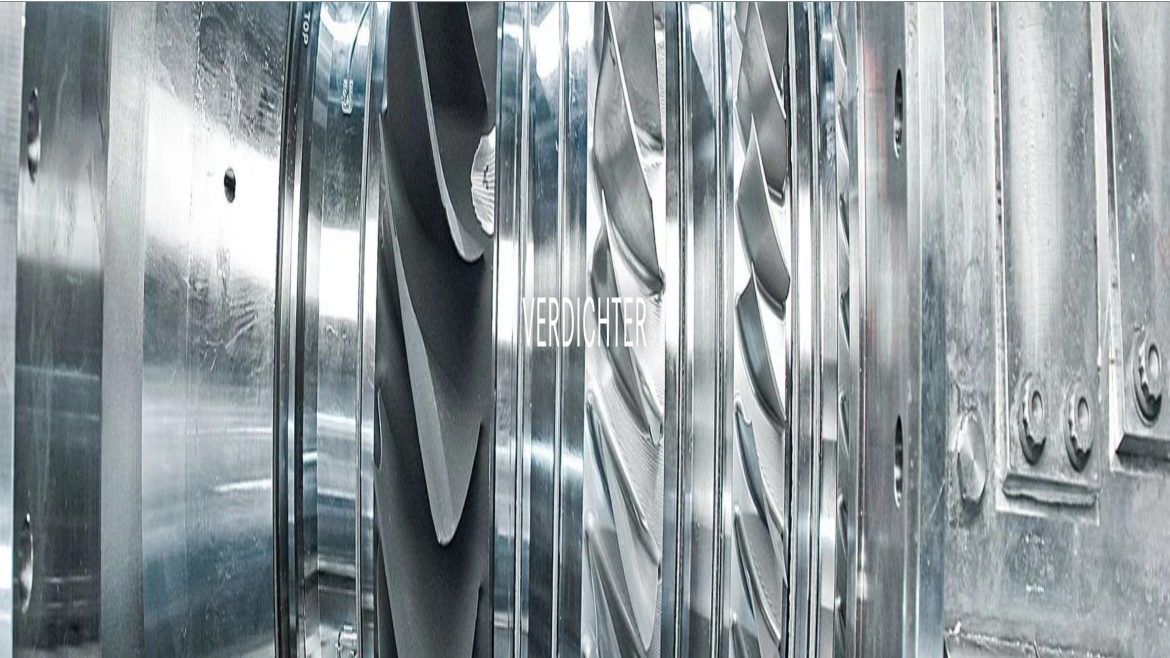
Running Duration:
01.08.2020 - 31.07.2023
Funded by:
- Federal Ministry for Economic Affairs and Climate Action, BMWi
- MTU Aero Engines AG
Project executing organisation:
Project Management Jülich
Project partners:
- Rheinisch Westfälische Technische Hochschule Aachen
- Technische Universität Berlin
- Technische Universität Dresden
- Universität Duisburg-Essen
- Leibniz Universität Hannover
- Technische Universität München
- Universität Stuttgart
- Deutsches Zentrum für Luft- und Raumfahrt e. V.
- MAN Energy Solutions SE
- MTU Aero Engines AG
- Rolls Royce Deutschland Ltd & Co. KG
- Siemens Energy Global GmbH & Co. KG