Laufzeit: 01.10.2021 - 30.09.2024
Projektpartner: Mühlbauer GmbH & Co. KG, Roding, Fraunhofer Gesellschaft e. V., München, rocon IT GmbH, Garching
Hintergrund
Die vierte industrielle Revolution soll die Produktion digitalisieren und intelligenter gestalten. Eine der Kernkomponenten der Industrie 4.0 sind prädiktive Wartungssysteme.
Durch eine kontinuierliche Überwachung von Kennwerten oder Anlagenteilen im laufenden Betrieb lassen sich Rückschlüsse auf deren Zustand ziehen. Verschiedene interne und externe Sensoren können zum Einsatz kommen, um Daten der Fertigungsanlage aufzunehmen. Wichtige Messgrößen sind dabei z. B. Ströme, Temperaturen, Beschleunigungen oder auftretende Kräfte.
Dieses durch den VDI/VDE-IT geförderte Projekt wird von einem Konsortium bestehend aus der Fraunhofer Einrichtung für Mikrosysteme und Festkörper-Technologien (EMFT), Procon IT GmbH, Mühlbauer GmbH und Hochschule für angewandte Wissenschaften München bearbeitet. Offizieller Beginn des Projekts war Oktober 2021, die Projektlaufzeit ist auf drei Jahre angesetzt.
Ziel
Ziel des Projekts ist es, mit einer limitierten Anzahl an Sensoren ein zuverlässiges prädiktives Wartungssystem zu erstellen, das ein anomales Verhalten einer Produktionsanlage erkennen kann. Neben dem aktuellen Betriebszustand können auch Rückschlüsse auf verbleibende Lebenszeit von Bauteilen gezogen werden. Zu den zu verwendeten Sensoren können Beschleunigungsmesser, Thermalelemente als auch bildgebende Sensoren gehören.
Methoden
Bestehende Verfahren sind auf spezielle Einsatzbereiche zugeschnitten. Im Rahmen dieses Projektes sollen verschiedene Methoden zum Einsatz kommen, um das Problem zu lösen. Neben klassischen Verfahren, wie Clusteringansätze oder statistische Modelle, werden überwachte und unüberwachte Trainingsalgorithmen basierend auf tiefen neuronalen Netzen verwendet. Auf letzteren soll ein besonderes Augenmerk liegen, da diese Netzwerke eine hohe Generalisierungsfähigkeit aufweisen und somit für die Aufgabe gut geeignet scheinen. Speziell generative Modelle finden in diesem Bereich noch kaum Einsatz, ihre Ergebnisse für vereinfachte Problemstellungen sind jedoch vielversprechend.
Um die optimale Lösung zu finden, müssen möglichst unterschiedliche Ansätze implementiert und evaluiert werden, bevor das prädiktive Wartungssystem bei den Produktionslinien Einsatz findet.
Eine Prädiktionskomponente basierend auf einem stochastischen Zuverlässigkeitsmodell soll bei der Bestimmung optimaler Wartungszeitpunkte helfen.
Herausforderungen
In realen Szenarien gibt es eine Vielzahl von Herausforderungen beim automatischen Detektieren von Anomalien. Zum einen kann nicht gewährleistet werden, dass Prozesse innerhalb einer Produktionslinie unabhängig voneinander ablaufen. Zudem stammen die Daten aus einer Vielzahl unterschiedlichster Quellen mit verschiedensten Wertedomänen. Sie sind multimodal. Eine weitere Schwierigkeit bereitet das Verarbeiten dieser Daten durch die stark unterschiedlichen Abtastraten. Je nach Sensortyp können Taktraten von wenigen Hertz bis mehreren Kilohertz auftreten.
Anomalien können in unterschiedlichen Formen auftreten: In Zeitreihen punktuell auftretende Ereignisse können auf einen Defekt eines Bauteils zurückzuführen sein. Beobachtet man Sensorwerte über einen längeren Zeitraum, kann ein sich ändernder Mittelwert eines Signals auf eine Degradierung hinweisen. Zudem können unbekannte, also noch nie beobachtete Fehlverhalten auftreten, die als Anomalien erkannt werden müssen.
Ein generelles Problem bei Datensätzen zur Anomaliedetektion ist das starke Ungleichgewicht der Daten, wodurch herkömmliche Klassifizierungsalgorithmen nicht zweckmäßig sind. Es kommt nicht selten vor, dass öffentliche Datensätze zu weit mehr als 90% aus Daten bestehen, die den Nominalzustand eines Bauteils oder einer ganzen Produktionsanlage beschreiben und nur wenige Beispiele vorhanden sind, die ein anomales Verhalten aufzeigen.
Das Aufnehmen eines Datensatzes in einer Produktivumgebung ist mit hohem zeitlichen und finanziellen Aufwand verbunden. Aus diesem Grund wird im Rahmen des Projekts zusätzlich ein Vorgehensmodell zur Modell- und Messgrößenauswahl entworfen.
Die Prädiktion der verbleibenden Lebenszeit stellt eine weitere Herausforderung dar. Hierzu werden existierende modellbasierte Verfahren zugrunde gelegt und auf den anwendungsfall adaptiert.
Ausblick
Ein neuartiges, generatives Modell zur Anomalieerkennung in Zeitreihen wurde bereits entworfen und anhand von öffentlich zugänglichen Referenzdatensätzen aus dem industriellen Umfeld validiert
Die nächsten Schritte legen eine Anpassung des Netzwerkes an reale Daten der Produktionsanlage nahe.
Zuwendungsgeber:
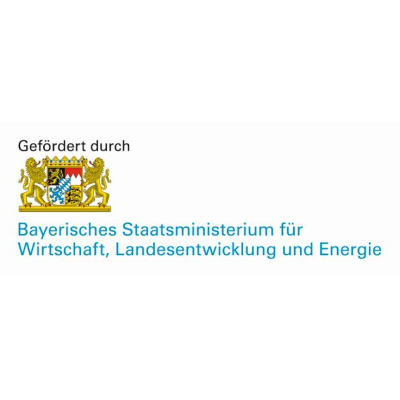